INNOVATION AND SUSTAINABILITY
INNOVATION AND SUSTAINABILITY
From its beginning, REV has proved itself to be particularly inclined to innovation: the first machine the company marketed, a punnet netting machine equipped with automatic tube change, that eliminated all machine stops, has, immediately, been patented.
Currently, all new REV’s projects are intended to accurately satisfy the market and customers’ demands and needs, also with ad-hoc solutions, capable of maximising the production or reducing the environmental impact by using a sustainable packaging. Therefore, REV invests 10% of its annual turnover in R&D.
INNOVATION
Our innovation takes shape through:
- Packaging evolution
The fruit and vegetable packaging industry is constantly evolving and new needs dictated by the large-scale distribution, related to innovative containers (more sustainable and attractive), are regularly appearing. These represent requirements different from those of the packagers, which must be able to satisfy the demand as quickly as possible and with maximum versatility. REV creates its machines with the purpose of filling the gap between the GDO’s and the packagers’ needs, always offering extremely advanced solutions.
- Versatility
REV thinks versatility is the key for the success of all of its models, especially inside a sector in which it is fundamental to best satisfy ever-more diversified requests coming from the global market. Some examples of great versatility are provided by Series U denesters, which can work all kinds of punnets and trays, both made of plastic or cardboard, in all formats and with clamshell closure as well, or by Vega horizontal netting machine (allowing to package a wide range of products, different in type or size) and by Condor, that permits to work both elongated produce (such as bananas, celeries and leeks) and spherical ones (melons, coconuts, small watermelons and pineapples).
- Performance increase
This is exactly the case of our Eagle and Condor automatic taping machines (which increase the taping speed by 350%, with respect to manual solutions adopted so far), of our Hollywood crate filming machine, able to simultaneously work more boxes, up to double the production, or our Bison, Velvet and Series A weighers which, thanks to their new software, can guarantee really high-level performances (+20% with respect to the previous versions) and more delicacy in treating the product.
- Production maximisation
REV, that always looks for solutions for saving time and money, continues investing on substituting its graphical interfaces with new-generation ones. Thanks to the new user-friendly interface, lots of functions (that needed to be manually set by the operator, so far) have now been automated and, as a result, the parameters necessary in order to start the work cycle significantly decreased. All REV’s new-graphical-interface machines can be equipped with advanced functions that conform with 4.0 Industry requirements and can be integrated inside SCADA control systems, also interfaced with third party’s machineries.
PATENTS
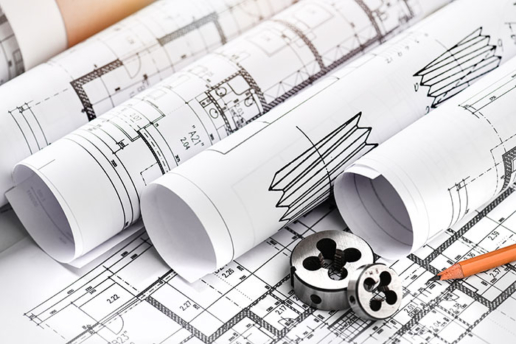
Some of REV’s most innovative projects have been patented. Currently, the list of patents the company filed includes:
- Bison and Velvet outfeed systems, allowing to work quicly and extremely delicately, at once;
- the completely automatic tube filling system of Genius net loader, which allows to significantly reduce production costs and labour and to load on the tube up to 30% more net;
- Rooster and Scorpion automatic crate filling systems, making the machines respectively 60% and 180% faster than traditional ones and allowing, in contrast to them, to work punnets with lid, in flowpack, netted and topseal, as well as to treat delicate produce (e.g. strawberries) without damaging them;
- Lion netting machine with thermosealing, which patent includes the punnet appearance as well.
SUSTAINABLE PACKAGING
Since ever, REV pays close attention to sustainability and packaging disposal issues. In fact, many of its innovative solutions, some of which have been patented, are intended to safeguard the environment.
This is especially the case of the netted punnets produced by Lion horizontal packaging machine in which, since 2010, the thermosealing technology substitutes the metal clip closure; as a result, the package is monomaterial and, thus, 100% recyclable.
In 2012, in the wake of the monomaterial punnets, REV created Tiger vertical packaging machine, in order to respond to the need of the UK’s large distribution of eliminating the clip from loose products packaged in line.
Between 2021’s news related to sustainability, Puma vertical netting machine represents the most relevant one: it realises monomaterial (with no metal clip) and 100%-recyclable packages, either in bag or in line, by using 50% less plastic with respect to super common Girsacs (quite heavy and non-recyclable) and maintaining the shape and benefits of traditional clipped nets which, to the present day, are considered to be the lightest packages on the market and, yet, are non-recyclable.
With all REV’s machines taking advantage of a thermosealing technology it is also possible to use certified compostable materials, instead of recyclable plastic ones.
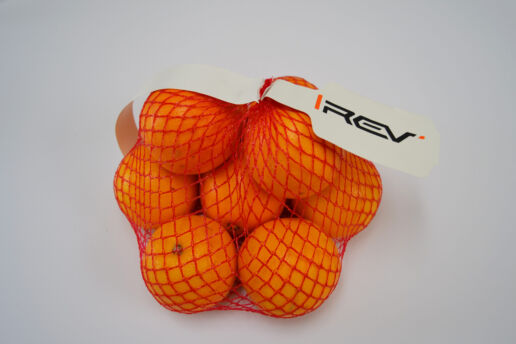